Demolition can be a complex and time-consuming task. It is important to choose a qualified demolition contractor who understands local and federal regulations and can complete the job on time. Quality contractors also keep up with technological developments that can assist them in their work. Contact Diversified Management & Construction, Inc. now!
Experts study the building’s construction materials, design, and usage before deciding on a demolition method. They also check for radioactive and flammable elements, including asbestos minerals and petroleum contamination.
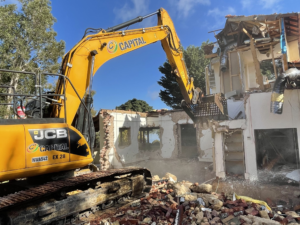
Demolition can be a dangerous process, so it’s important to take steps to protect workers and avoid accidents. In addition to ensuring that equipment is in good working condition, it’s also important to have a clear plan for how the demolition will be conducted and to train employees on how to operate machinery safely. Common demolition hazards include being hit by falling debris, exposure to hazardous air contaminants, and electrical shock.
When preparing for demolition, businesses should ensure that their contractors are qualified to perform the work safely. This includes making sure that all employees have undergone appropriate training courses and have the right qualifications to operate demolition machinery. Additionally, a risk assessment should be completed before demolition begins to identify any potential hazards and determine how they will be mitigated.
To prevent accidental fires, contractors should enclose all demolition areas with fencing and barricades to restrict access to the site and prevent unauthorized entry. Workers should be given safety helmets, eye protection, and personal protective equipment to wear when operating machinery. They should also receive regular safety briefings and have real-time communication tools to alert them of any dangers onsite.
In addition to physical barriers, a demolition contractor should secure the site by shutting off all utilities. This includes shutting off water, sewer, and gas. It’s also a good idea to notify local authorities and utility companies of the planned demolition activities and to post emergency telephone numbers at all locations.
Airborne hazards such as dust and chemical vapors can pose significant risks during demolition. Construction professionals can minimize this by conducting air quality assessments and implementing control measures to limit exposure, such as ventilation systems and wetting surfaces.
In addition, confined spaces pose many risks and should be avoided when possible. These spaces include vessels, storage tanks, pits vaults, silos, and degreasers. They may be flooded, poisonous, or contain asphyxiant gases. Regardless of their size, they should be entered only by authorized personnel and equipped with proper breathing and rescue equipment. In addition, they should be monitored with a combustible gas indicator, toxic gas monitor, and oxygen monitor.
Reputation
The reputation of demolition equipment is important, as it can impact the safety and effectiveness of a project. It’s important to find a company with a solid track record, as well as one that is known for being transparent and easy to work with. Many demolition companies are able to provide references from previous clients, so be sure to ask for them.
In addition, you should look for a company that has experience working on the type of structure you are looking to demolish. Different structures require specialized equipment, so it’s important to find a company that is familiar with your project’s needs.
Also, any materials and debris from a demolition project must be transported off-site for disposal, recycling, or reuse. This is where dump trucks come in handy, as they can load the debris right into them, and then drive it off-site to a landfill or recycling facility.
Equipment
Whether you are doing a small DIY renovation or tearing down a large structure, the right equipment can make all the difference. From essential hand tools like sledgehammers to powerful machinery like excavators, there are a variety of different demolition equipment types available to suit your specific needs. This article will explore the basics of each type, including how it works, its advantages, and disadvantages. It will also cover tips for choosing the right equipment, ensuring safety, and complying with local regulations.
The first step in any demolition project is to evaluate the site and determine what work is needed. This can involve identifying asbestos, lead paint, structural weaknesses, and other potential hazards. Once this is complete, the demolition can begin. This is a critical step, and it should be performed by an experienced professional. It is also important to check that all utilities are disconnected before the demolition begins, as the process can be dangerous if these services are still active.
Before starting demolition, it is a good idea to get a permit from your local city or county. You should also check the demolition company’s credentials and licenses before hiring them. You can do this by researching the company online or asking for referrals from family and friends. Make sure to select a company with extensive experience in commercial and residential demolition.
Demolition is a complex process that requires the use of specialized equipment. The equipment can include skid steers, bulldozers, wheel loaders, and excavators. Skid steers are smaller and more maneuverable than other pieces of machinery, making them ideal for small projects. They can also be fitted with different attachments for more specific jobs.
Bulldozers are an essential piece of equipment for any demolition project. They can be equipped with a blade at the front and a ripper at the back, and are used for a wide range of tasks including land clearing, grading, and scraper work. They are also great for moving debris around a site.
For larger buildings, you may want to use an excavator with attachments like shears or hydraulic breakers. For high-rise demolitions, a crane is often required. These machines are especially effective for removing metals from demolished structures.
Cost
A demolition project can be a costly one, especially when it comes to the cost of the equipment involved. However, with careful planning and understanding the average costs per square foot of different types of projects, you can ensure that your budget is on track. There are two main options available to property owners when it comes to changing the look or layout of a building: renovating and demolishing. Both offer advantages, but the choice may come down to the costs involved.
The cost of demolition equipment can vary significantly based on the type of structure being demolished, its square footage, and the type of construction materials. In general, the more complicated and large a structure is, the more expensive it will be to tear down. This is because larger structures require more manpower, time, and machinery to dismantle. On the other hand, smaller structures can be less expensive as they don’t require as much manpower and time to demolish.
Demolition costs can be a significant cost for property owners, and it is important to know what to expect when hiring a demolition company. In addition to the cost of the equipment, there are other costs such as permits and cleanup fees. Depending on the location, permits can range from a few hundred dollars to as much as $10,000.
There are a few basic formulas that can be used to estimate the demolition costs of a particular structure. For example, a metal structure that is bolted together with a cosmetic skin can be quite simple to tear down and will only cost about $2 per square foot. On the other hand, a brick building that requires special attention to remove asbestos could cost up to $7 per square foot.
In order to develop a successful demolition estimate, it is important to use the organization’s past performance data and check and double-check all items that will affect the price of the project. This will help to prevent costly mistakes that can result in a lost profit or a loss for the client.
In the demolition industry, it is possible to make a large profit or lose an equal amount of money based on a project’s actual costs and production rates. This volatility creates an environment that is challenging for any contractor, but it is possible to reduce the risk by developing a system for tracking and reporting real-time cost information.